One small step for an amputee and a giant leap for Amparo and GDI Hub
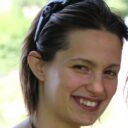
30th July 2019
I have been a physio long before I became a researcher and, to this day, I still consider myself a clinician at heart. That is probably why I am always very happy to take the lead on more clinical research projects that would be at the bottom of the “favourite” list of a lot of my fellow HCI (Human Computer Interaction) researchers. Don’t get me wrong, I do get excited about mobile phones and various apps as much as the next person, but I’ll pick a wheelchair or a prosthesis over them any day of the week. For this reason I count myself very lucky to have had the opportunity to spend one week in Mombasa, Kenya with Amparo GmbH and the Association for the Physically Disabled of Kenya (APDK) working on a new project on lower limbs prosthetics that is part of the AT2030 programme.
Most of us who live in Western society are mainly exposed to prosthetics through mainstream sport events such as the Paralympic Games or the World Para Athletics Championships. As a consequence, we imagine many amputees to be running on their blades at incredible speeds like Blake Leeper. The reality is that most people who undergo a leg amputation don’t have access to a standard prosthesis (never mind a racing blade), and this is especially true in low and middle income countries like Kenya. Like for all other Assistive Tech products, the reasons for this lack of access are many, but the long and convoluted manufacturing process of prosthetic limbs is definitely an important factor.
A prosthetic leg is roughly made of three different parts: a foot, which shape and function are pretty much implied in the name; a pylon, a metallic or plastic part that connects the foot to the leg of the person; and a socket, that is a plastic cup that attaches directly to the leg of the person. The foot and pylons are usually standard components that can be purchased and pretty much used off-the shelf. A socket, on the other hand, has to be custom-made and it’s usually hand-made over a couple of days by a qualified prosthetic technician. Making a prosthetic socket is a complex procedure that involves, several steps, multiple visits with clients and expensive specialized tools.
Since I first heard about the Amparo Confidence socket, during the Enable Makeathon 2.0 hosted by GDI Hub in 2017, I knew that their innovative approach had the potential to be revolutionary. A new prosthetic socket made of thermoplastic material that could be warmed up with a heat gun and moulded directly on the patient in less than 2 hours? It was simply incredible. Having followed their journey from a distance for over a year, I was really happy when, about 6 months ago, I got the opportunity to work closely with the Amparo team to design a research protocol to evaluate the impact of the Confidence socket in Kenya.
After much hard work behind the scenes, the trial finally kicked off on the 8th of July at APDK in Mombasa and on the 15th of July at the Cure Hospital in Kijabe. As the week started, I was really nervous. The timing was tight and there was little room for errors if we wanted to start the trial on the right foot. A misunderstanding about location that saw myself and the Amparo team showing up on Monday morning at the wrong address did not do much to relax my nerves. However, as soon as we started the training with the technicians at APDK I felt better. I am no prosthetic technician, but I can recognize a good healthcare professional when I meet one and the technicians at APDK were clearly skilled and eager to learn.
With no time to lose we started to see the first clients on the morning of the Tuesday. I am always blown away by the resourcefulness and insight of people with disabilities around the world and this time it was no different. Some of the clients had a prosthetic leg that needed to be changed, while others had undergone amputations a few years back and they were still waiting for they prosthetic legs as there hasn’t been any funding available to cover the cost of fabrication. Still, regardless of the availability of a prosthetic leg, they all went on with their personal lives, engaged with their communities and worked to help sustain their families.
All participants were curious about the research and the technology and looked forward to receiving a new prosthetic leg. But most of them were also a bit doubtful about this group of “Wazungu” (white people) who arrived in Kenya with a lot of promises and requests. The most satisfying part for me was to see how people’s expressions changed throughout the week as we explained the research, moulded the sockets and finally fitted the new prosthesis. During the various activities, participants got to know us as much as we got to know them and, together with the technicians at APDK, we looked at how smiles slowly replaced the sceptical expressions that we saw at the beginning of the week.
As I watched one of our clients take her first steps on her own two feet since her amputation three years ago I could not help but think that this was truly a giant leap for us.
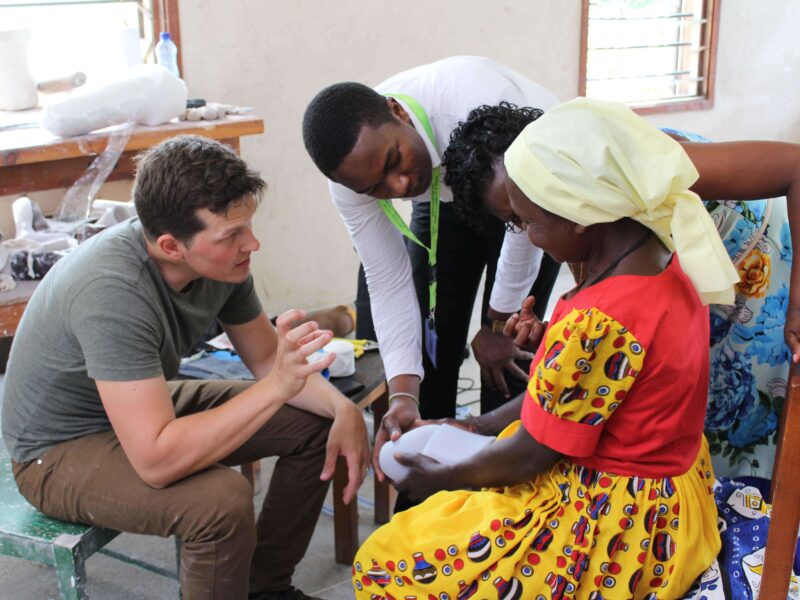